High Quality For 201 Stainless Steel Coil - Royal Group 201 304 316 304L 316L Seamless Stainless Steel Pipe – Royal Group
High Quality For 201 Stainless Steel Coil - Royal Group 201 304 316 304L 316L Seamless Stainless Steel Pipe – Royal Group Detail:
Product Detail
Product Name | Stainless steel Round pipe |
Standard | ASTM AISI DIN, EN, GB, JIS |
Steel Grade
|
200 Series: 201,202 |
300 Series: 301,304,304L,316,316L,316Ti,317L,321,309s,310s | |
400 Series: 409L,410,410s,420j1,420j2,430,444,441,436 | |
Duplex Steel: 904L,2205,2507,2101,2520,2304 | |
Outer Diameter | 6-2500mm(as required) |
Thickness | 0.3mm-150mm (as required) |
Length | 2000mm/2500mm/3000mm/6000mm/12000mm(as required) |
Technique | Seamless |
Surface | No.1 2B BA 6K 8K Mirror No.4 HL |
Tolerance | ±1% |
Price Terms | FOB,CFR,CIF |
Main Application
Stainless steel pipe is a kind of hollow long round steel, which is mainly used in industrial transportation pipelines such as petroleum, chemical industry, medical treatment, food, light industry, mechanical instrument, etc., as well as mechanical structural components. In addition, when the bending and torsional strength are the same, the weight is lighter, so it is also widely used in the manufacture of mechanical parts and engineering structures. Also commonly used as furniture and kitchenware, etc.
Note:
1.Free sampling, 100% after-sales quality assurance, Support any payment method;
2.All other specifications of round carbon steel pipes are available according to your requirement (OEM&ODM)! Factory price you will get from ROYAL GROUP.
Stainless Steel Pipe Chemical Compositions
Through different processing methods of cold rolling and surface reprocessing after rolling, the surface finish of stainless steel bars can have different types.
The surface processing of stainless steel coils have NO.1, 2B, No. 4, HL, No. 6, No. 8, BA, TR hard, Rerolled bright 2H, polishing bright and other surface finishes, etc.
NO.1: No. 1 surface refers to the surface obtained by heat treatment and pickling after hot rolling of the stainless steel strip. It is to remove the black oxide scale produced during hot rolling and heat treatment by pickling or similar treatment methods. This is No. 1 surface processing. The No.1 surface is silvery white and matt. Mainly used in heat-resistant and corrosion-resistant industries that do not require surface gloss, such as alcohol industry, chemical industry and large containers.
2B: The surface of 2B is different from the 2D surface in that it is smoothed with a smooth roller, so it is brighter than the 2D surface. The surface roughness Ra value measured by the instrument is 0.1~0.5μm, which is the most common processing type. This kind of stainless steel strip surface is the most versatile, suitable for general purposes, which is widely used in the chemical, paper, petroleum, medical and other industries, and can also be used as a building curtain wall.
TR Hard Finish: TR stainless steel is also called hard steel. Its representative steel grades are 304 and 301, they are used for products that require high strength and hardness, such as railway vehicles, conveyor belts, springs and gaskets. The principle is to use the work hardening characteristics of austenitic stainless steel to increase the strength and hardness of the steel plate by cold working methods such as rolling. The hard material uses a few percent to several tens of percent of the mild rolling to replace the mild flatness of the 2B base surface, and no annealing is carried out after rolling. Therefore, the TR hard surface of the hard material is the rolled after cold rolling surface.
Rerolled Bright 2H: After the rolling process. the stainless steel strips will be processed bright annealing. The strip can be fast cooled by the the continuous annealing line. The traveling speed of the stainless steel strip on the line is around 60m~80m/min. After this step, the surface finish will be 2H rerolled bright.
No.4: The surface of No. 4 is a fine polished surface finish that is brighter than the surface of No. 3. It is also obtained by polishing the stainless steel cold-rolled stainless steel plate with 2 D or 2 B surface as the base and polishing with abrasive belt with a grain size of 150-180# Machined surface. The surface roughness Ra value measured by the instrument is 0.2~1.5μm. NO.4 surface is widely used in restaurant and kitchen equipment, medical equipment, architectural decoration, containers, etc.
HL: HL surface is commonly called hairline finish. Japanese JIS standard stipulates that 150-240# abrasive belt is used to polish the continuous hairline-like abrasive surface obtained. In China’s GB3280 standard, the regulations are rather vague. HL surface finish is mostly used for building decoration such as elevators, escalators, and facades.
No.6: The surface of No. 6 is based on the surface of No. 4 and is further polished with a Tampico brush or abrasive material with a particle size of W63 specified by GB2477 standard. This surface has a good metallic luster and soft performance. The reflection is weak and does not reflect the image. Due to this good property, it is very suitable for making building curtain walls and building fringe decorations, and also widely used as kitchen utensils.
BA: BA is the surface obtained by bright heat treatment after cold rolling. Bright heat treatment is annealing under a protective atmosphere that guarantees that the surface is not oxidized to preserve the gloss of the cold-rolled surface, and then use a high-precision smoothing roll for light leveling to improve the surface brightness. This surface is close to a mirror finish, and the surface roughness Ra value measured by the instrument is 0.05-0.1μm. BA surface has a wide range of uses and can be used as kitchen utensils, household appliances, medical equipment, auto parts and decorations.
No.8: No.8 is a mirror-finished surface with the highest reflectivity without abrasive grains. The stainless steel deep processing industry also calls as 8K plates. Generally, BA materials are used as raw materials for mirror finishing only through grinding and polishing. After mirror finishing, the surface is artistic, so it is mostly used in building entrance decoration and interior decoration.
Main production process: round steel → re-inspection → peeling → blanking → centering → heating → perforation → pickling → flat head → inspection and grinding → cold rolling (cold drawing) → degreasing → heat treatment → straightening → pipe cutting (fixed-to-length) )→pickling/passivation→finished product inspection (eddy current, ultrasonic, water pressure)→packaging and storage.
1. Round steel cutting: After receiving the round steel from the raw material warehouse, calculate the cutting length of the round steel according to the requirements of the process, and draw a line on the round steel. Steels are stacked according to steel grades, heat numbers, production batch numbers and specifications, and the ends are distinguished by paints of different colors.
2. Centering: When centering the cross arm drilling machine, first find the center point in a section of the round steel, punch out the sample hole, and then fix it vertically on the drilling machine table for centering. The round bars after centering are stacked according to steel grade, heat number, specification and production batch number.
3. Peeling: peeling is carried out after passing the inspection of the incoming materials. The peeling includes lathe peeling and whirlwind cutting. The lathe peeling is carried out on the lathe by the processing method of one clamp and one top, and the whirlwind cutting is to hang the round steel on the machine tool. Perform whirling.
4. Surface inspection: The quality inspection of the peeled round steel is carried out, and the existing surface defects are marked, and the grinding personnel will grind them until they are qualified. The round bars that have passed the inspection are piled up separately according to the steel grade, heat number, specification and production batch number.
5. Round steel heating: Round steel heating equipment includes gas-fired inclined hearth furnace and gas-fired box-type furnace. Gas-fired inclined-heart furnace is used for heating in large batches, and gas-fired box-type furnace is used for heating in small batches. When entering the furnace, the round bars of different steel grades, heat numbers and specifications are separated by the old outer film. When the round bars are heated, the turners use special tools to turn the bars to ensure that the round bars are heated evenly.
6. Hot rolling piercing: use piercing unit and air compressor. According to the specifications of the perforated round steel, the corresponding guide plates and molybdenum plugs are selected, and the heated round steel is perforated with a perforator, and the pierced waste pipes are randomly fed into the pool for full cooling.
7. Inspection and grinding: Check that the inner and outer surfaces of the waste pipe are smooth and smooth, and there must be no flower skin, cracks, interlayers, deep pits, serious thread marks, tower iron, fritters, Baotou and sickle heads. The surface defects of the waste pipe can be eliminated by the local grinding method. The waste pipes that have passed the inspection or those that have passed the inspection after repairing and grinding with minor defects shall be bundled by the workshop bundlers according to the requirements, and stacked according to the steel grade, furnace number, specification and production batch number of the waste pipe.
8. Straightening: The incoming waste pipes in the perforation workshop are packed in bundles. The shape of the incoming waste pipe is bent and needs to be straightened. The straightening equipment is vertical straightening machine, horizontal straightening machine and vertical hydraulic press (used for pre-straightening when the steel pipe has a large curvature). In order to prevent the steel pipe from jumping during straightening, a nylon sleeve is used to limit the steel pipe.
9. Pipe cutting: According to the production plan, the straightened waste pipe needs to be cut head and tail, and the equipment used is a grinding wheel cutting machine.
10. Pickling: The straightened steel pipe needs to be pickled to remove the oxide scale and impurities on the surface of the waste pipe. The steel pipe is pickled in the pickling workshop, and the steel pipe is slowly hoisted into the pickling tank for pickling by driving.
11. Grinding, endoscopy inspection and internal polishing: the steel pipes that are qualified for pickling enter the outer surface grinding process, the polished steel pipes are subjected to endoscopic inspection, and the unqualified products or processes with special requirements need to be internally polished deal with.
12. Cold rolling process/cold drawing process
Cold rolling: The steel pipe is rolled by the rolls of the cold rolling mill, and the size and length of the steel pipe are changed by continuous cold deformation.
Cold drawing: The steel pipe is flared and wall-reduced with a cold drawing machine without heating to change the size and length of the steel pipe. The cold-drawn steel pipe has high dimensional accuracy and good surface finish. The disadvantage is that the residual stress is large, and Large-diameter cold-drawn pipes are frequently used, and the finished product forming speed is slow. The specific process of cold drawing includes:
① Heading welding head: Before cold drawing, one end of the steel pipe needs to be headed (small diameter steel pipe) or welding head (large diameter steel pipe) to prepare for the drawing process, and a small amount of special specification steel pipe needs to be heated and then headed.
② Lubrication and baking: Before the cold drawing of the steel pipe after the head (welding head), the inner hole and outer surface of the steel pipe shall be lubricated, and the steel pipe coated with lubricant shall be dried before cold drawing.
③ Cold drawing: The steel pipe after the lubricant is dried enters the cold drawing process, and the equipment used for cold drawing is a chain cold drawing machine and a hydraulic cold drawing machine.
13. Degreasing: The purpose of degreasing is to remove the rolling oil attached to the inner wall and outer surface of the steel pipe after rolling by rinsing, so as to avoid contaminating the surface of the steel during annealing and preventing carbon increase.
14. Heat treatment: Heat treatment restores the shape of the material through recrystallization and reduces the deformation resistance of the metal. The heat treatment equipment is a natural gas solution heat treatment furnace.
15. Pickling of finished products: The steel pipes after cutting are subjected to finished pickling for the purpose of surface passivation, so that an oxide protective film can be formed on the surface of the steel pipes and enhance the excellent performance of the steel pipes.
16. Finished product inspection: The main process of finished product inspection and test is meter inspection → eddy probe → super probe → water pressure → air pressure. The surface inspection is mainly to manually check whether there are defects on the surface of the steel pipe, whether the length of the steel pipe and the size of the outer wall are qualified; the eddy detection mainly uses the eddy current flaw detector to check whether there are loopholes in the steel pipe; the super-detection mainly uses the ultrasonic flaw detector to check whether the steel pipe is cracked inside or outside; the water pressure , Air pressure is to use hydraulic machine and air pressure machine to detect whether the steel pipe leaks water or air, so as to ensure that the steel pipe is in good condition.
17. Packing and warehousing: The steel pipes that have passed the inspection enter the finished product packaging area for packaging. The materials used for packaging include hole caps, plastic bags, snakeskin cloth, wooden boards, stainless steel belts, etc. The outer surface of both ends of the wrapped steel pipe is lined with small wooden boards, and the outer surface is fastened with stainless steel belts to prevent the contact between the steel pipes during transportation and cause collision. Packaged steel pipes enter the finished product stacking area.
Packing and Transportation
Packaging is generally naked, steel wire binding, very strong.
If you have special requirements, you can use rust proof packaging, and more beautiful.
Transportation: Express (Sample Delivery), Air, Rail, Land, Sea shipping (FCL or LCL or Bulk)
Our Customer
FAQ
Q: Are u a manufacturer?
A: Yes, we are spiral steel tube manufacturer locates in Daqiuzhuang village, Tianjin city, China
Q: Can I have a trial order only several tons?
A: Of course. We can ship the cargo for u with LCL serivece.(Less container load)
Q: Do u have payment superiority?
A: For big order, 30-90 days L/C can be acceptable.
Q: If sample free?
A: Sample free, but the buyer pays for the freight.
Q: Are you gold supplier and do trade assurance?
A: We seven years cold supplier and accept trade assurance.
Product detail pictures:
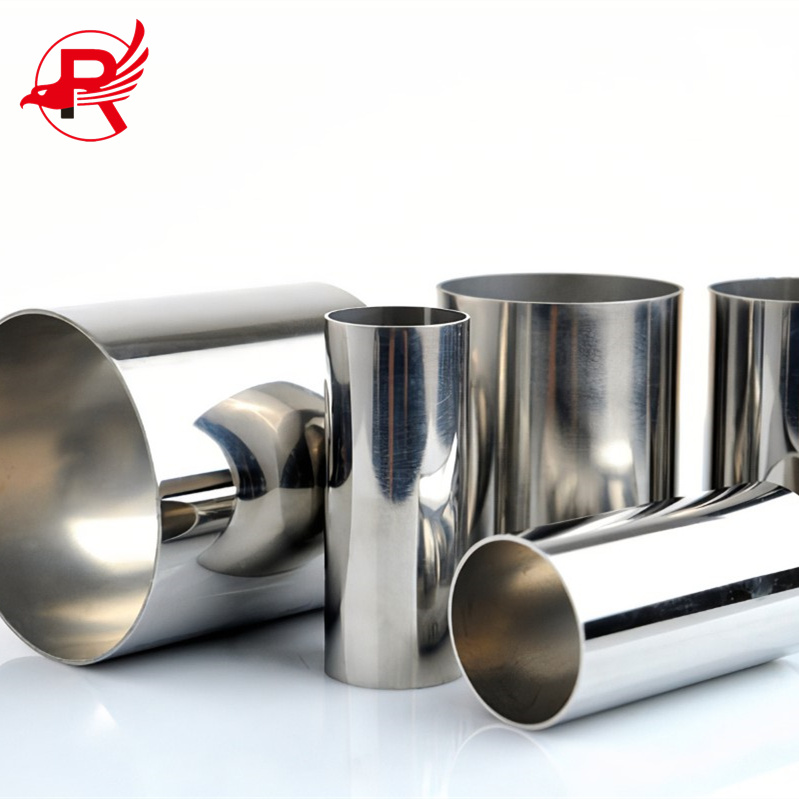


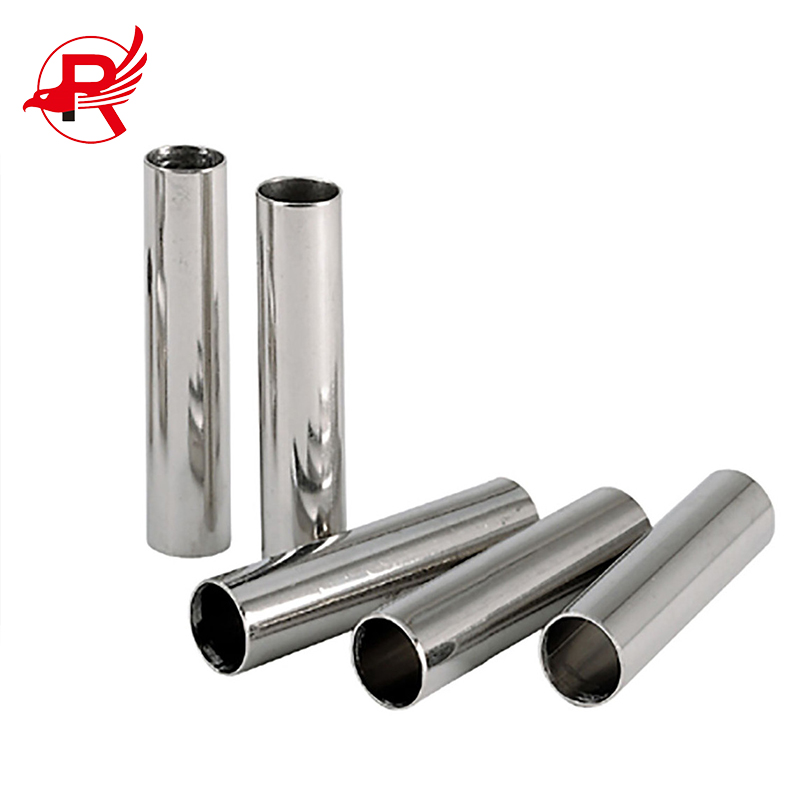
Related Product Guide:
Sticking towards the theory of Super Good quality, Satisfactory service ,We are striving to become a superb business enterprise partner of you for High Quality For 201 Stainless Steel Coil - Royal Group 201 304 316 304L 316L Seamless Stainless Steel Pipe – Royal Group , The product will supply to all over the world, such as: St. Petersburg, Berlin, Lahore, We welcome customers from all over the world come to discuss business. We supply high quality products, reasonable prices and good services. We hope to sincerely build business relationships with customers from at home and abroad, jointly striving for a resplendent tomorrow.

Production management mechanism is completed, quality is guaranteed, high credibility and service let the cooperation is easy, perfect!
